Biomass Dust Suppression System Upgrade
Situation
This 44 MW Biomass Power Station in California, USA, was experiencing excessive fugitive dusting during off-loading of biomass fuel trucks to the boom stackout conveyor. For this reason, the plant used water sprays at five locations in the conveying process to try to control dusting, with unacceptable results. As the plant is committed to safety and focused on ensuring environmental compliance, they needed a solution to address this unacceptable condition. Therefore, under these extremely dusty conditions, they added 10-12% moisture (by weight) to control the dust.
Existing Problems
- Unacceptable fugitive dust emissions
- Excessive water usage
- Ineffective dust control
- Increased moisture reduces heat rate for power generation
- Degradation/fouling of material during storage
- Belt tracking issues due to wet conveyor belts
- Excessive carryback and build-up in the conveying system
- High maintenance with clogged nozzles in difficult to reach areas
The Benetech Solution
The new Benetech Engineered Dust Suppression System improved and simplified application to one location at grade, providing ease of maintenance. In addition, this new system lowered the moisture addition to less than 2% by weight by incorporating a Benetech Dust Suppression agent. The system utilized Benetech’s BT-205W, blended at a high dilution ratio with low BT-205W usage rates. This high-quality surfactant blend works by providing a means of rapid wetting of hard to control dust particles, then agglomerating the dust to the larger particles and keeping it from getting airborne in the first place.
And so, the solution was applied at the truck dump feeders and maintained its residual effects to control dust through the conveying process and to stackout on the pile. As a result, the system lowered water usage, improved application, and lowered maintenance of the spray system and cleanup in the conveying system. Then, upon installation, it continues to provide a drastic reduction in dust emissions. As noted by personnel at the site, the difference was “night and day!”
Successful Results
- Dust levels reduced by over 90%
- Eliminated need for existing hard to maintain spray system
- Reduced moisture addition to less than 2%
- Improved access for maintenance
- Reduced moisture addition improved heat rate
- Reduced maintenance issues with build-up
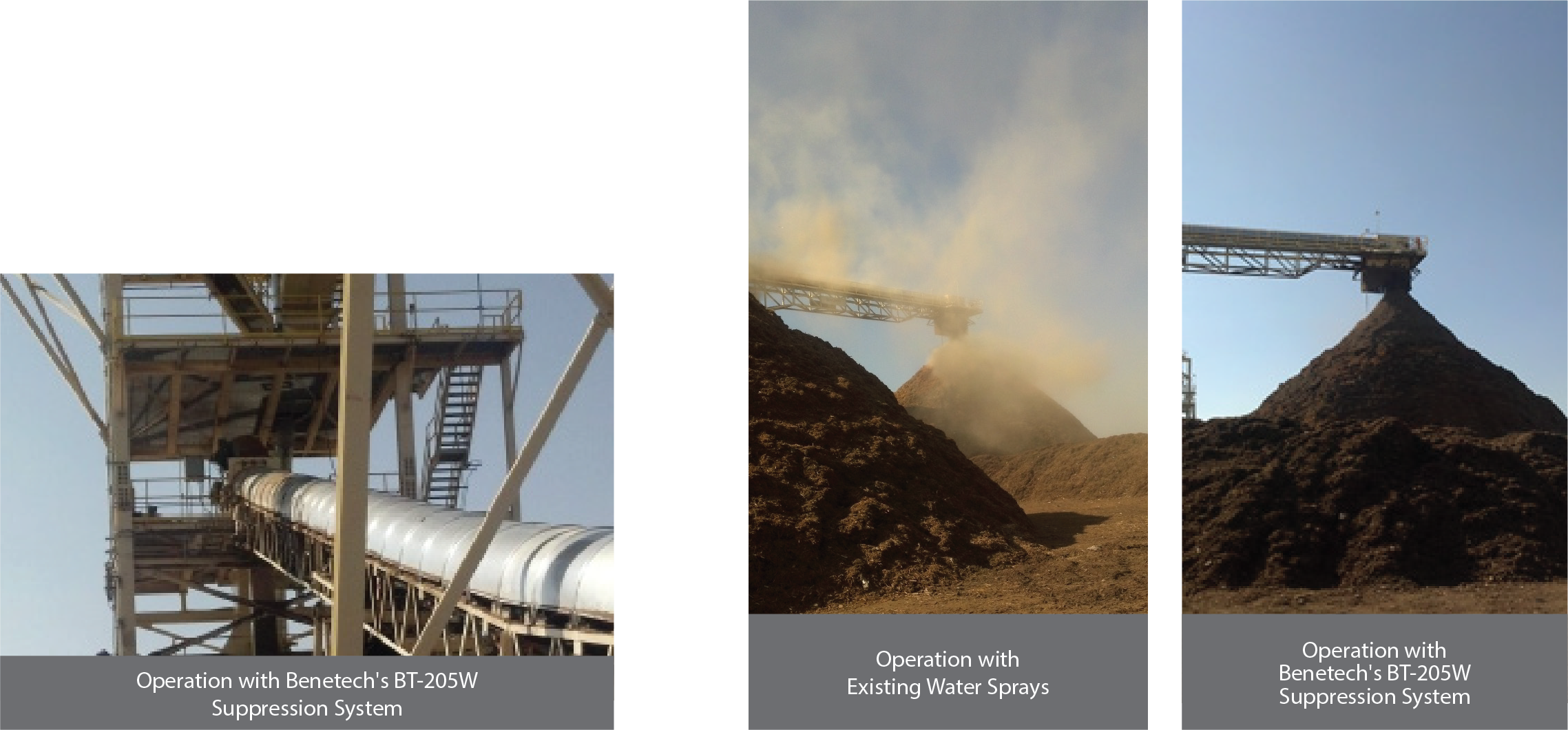