
Utility to Implement Life Cycle Upgrades for Improved Safety and Material Efficiency
Situation
Entergy Nelson was at a crossroads with much of its material handling operation, having met life expectations. The result of this aging system was spillage and dust generation and excessive requirements for ongoing maintenance and housekeeping. The plant knew that changes needed to be made. As part of its ongoing focus on safety, Entergy Nelson conducted internal reviews and identified several areas that needed to be addressed. With a desire for a safe workplace and efficient operation, the plant management and operating team took the safety audit results very seriously. They were committed to improving their plant and decided to partner with Benetech to develop and prioritize a plan to get the plant into compliance.
Benetech Approach
To get a handle on current operations and challenges, Benetech did a full assessment of the plant’s material handling operation. Based on the initial audit results and discussions with plant personnel, Benetech created a work scope to address the noted issues. The scope of work was prioritized and then divided into organized sections. Benetech was able to work with plant personnel and develop a go-forward game plan, which allowed the plant to evaluate and select several projects to improve safety and efficiency. As a result, many projects have been completed while new projects continue to move forward.
Scope of Work
Benetech’s Design-Build Group supplied turnkey service in completing several upgrades and has provided management and oversight to ensure the projects meet the intent plant goals. These projects include:
- Emergency Stackout Conveyor Replacement
- Crusher Transfer Upgrade including New Loading to Emergency Conveyor
- Existing Crusher Replacement
- Washdown System
- Engineered Retaining Wall System
- Conveyor Guarding Installation
Ongoing Projects include additional conveyor guarding and an engineered turnkey material handling system for the rail car dumper to replace the existing vibratory feeders with new posimetric feeders. This project includes:
- Supply (4) new posimetric feeders to replace the existing (6) vibratory feeders
- RCD Hopper replacement and grizzly deck modifications
- Engineered structural steel modifications
- New chute work from hoppers to new posimetric feeders
- New chute work from posimetric feeders to conveyor 1
- Load Zone modifications on conveyor 1
Solution Achieved
After one year of work, Entergy again conducted an internal review of the Nelson plant, which showed the significant improvement that had been achieved. This committed plant leadership team took the safety audit very seriously and did what was needed to achieve these positive results. They are a true example of how best to run a plant of this magnitude. Benetech supports the plant team in the successful implementation of the life cycle upgrades and is committed to ensuring that Entergy Nelson becomes one of the safest and most reliable plants in the United States.


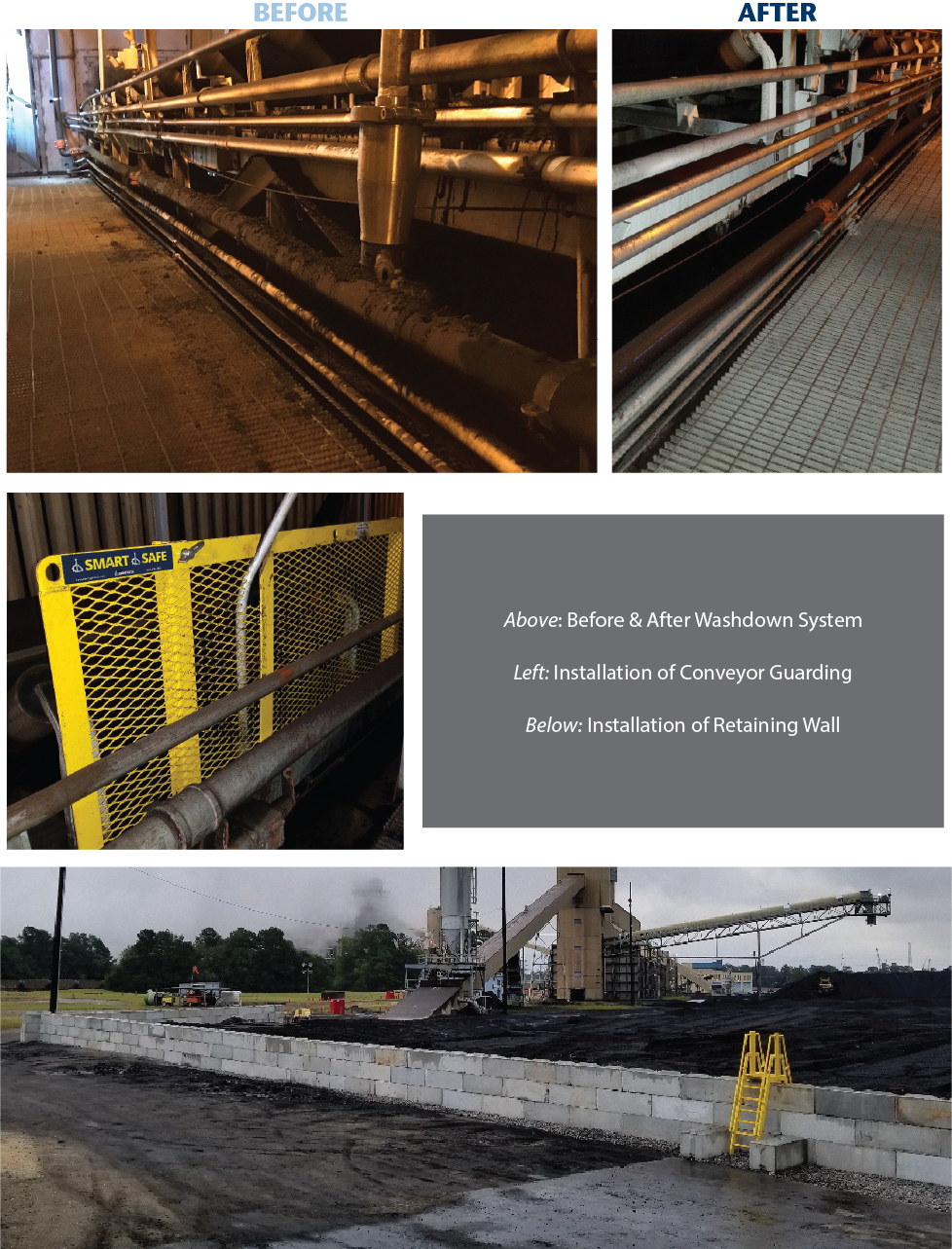