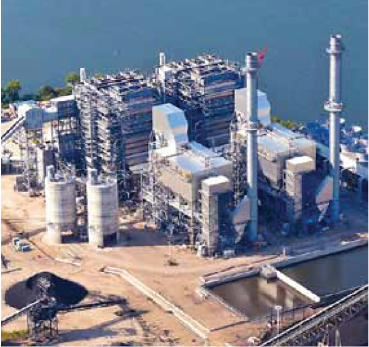
Situation
When Luminant retired three old units at the Sandow Power Plant, Sandow generated plans to build a new, efficient Unit 5 on the site. However, to control overall costs on the project, the plant decided to review the existing handling system and see if a new system would be necessary or upgrade the existing coal handling system that fed the decommissioned units to feed the new units efficiently.
Project Profile
Luminant operates several mines and power plants in Texas and is the largest power producer and the largest lignite coal miner in the State of Texas. At the start of the project, Luminant solicited bids from several companies to assess the current condition of the system and get an idea of the costs required to bring this system back into an efficient and reliable service. Benetech was the successful bidder to conduct the assessment.
Based on the assessment results, Luminant decided they could utilize the existing system based on the upgrades outlined by the Benetech team, saving costs and fitting within the scheduled start-up of the new units. Following the assessment, Benetech was further able to negotiate with the Sandow team to manage and implement many of the upgrades noted during the initial assessment, including managing the upgrade process, conducting design and fabrication of the equipment, and running the installation and start-up of the systems.
The Benetech EPC Approach
Benetech’s Plant Professional division conducted the initial review of the coal handling system, providing a report that focused on the right technology solutions without recommending manufacturers or equipment models. The entire handling system was reviewed, including all components of the system. This consisted of receiving coal from the mine conveyor through stackout, reclaim, crushing, then tying into a new conveyor that brought the fuel to the new unit.
The assessment team consisted of experts in coal handling, operations, dust control, maintenance, mechanical design, electrical design, chute work, and containment system design. Each person added to the credibility of the assessment, avoiding the need for individuals to operate outside their area of expertise. In addition, each team member contributed to the project’s overall success based on extensive experience in their specific area and integration in the handling of coal.
Solution Achieved
Upon completion of the assessment, the utility was able to understand the condition of the handling system. As a result, it was able to prioritize projects based on need as well as available capital. This allowed station management to properly budget for the projects with the confidence that they were covered for their undertaking.
After the assessment, the team was able to successfully negotiate with Luminant to move forward with the upgrades that the station team chose to move forward with. Benetech provided project management to oversee the process, engineering design support, fabrication, equipment supply, installation, start-up, and training of the plant personnel.
Upgrades For The Handling System Included:
- Eight chutes
- Containment upgrades to ten conveyors
- Clean Sweep Air Cannon installation in four chutes
- Fifteen Midcap projects (conveyor evaluation, upgrade capacity of stackout, take-up re-engineering, re-work of the stacker)
- Dust Suppression System
- Benetech partnered with an engineering firm to complete the necessary balance of plant system upgrades as well. As a result, material flow is now controlled, drastically reducing dust generation.
